Zehaztasuna piezaren produktuaren fintasuna adierazteko erabiltzen da. Mekanizatutako gainazalaren parametro geometrikoak ebaluatzeko termino berezia da. CNC mekanizazio zentroen errendimendua neurtzeko adierazle garrantzitsua ere bada. Oro har, mekanizazio-zehaztasuna tolerantzia-mailen arabera neurtzen da. Zenbat eta maila baxuagoa izan, orduan eta zehaztasun handiagoa. Torneatzea, fresatzea, planeatzea, arteztea, zulatzea eta mandrinatzea CNCko mekanizazio-zentroetako prozesatzeko forma arruntak dira. Beraz, zer prozesatzeko zehaztasuna lortu behar dute prozesatzeko prozedura hauek?
1.Turning zehaztasuna
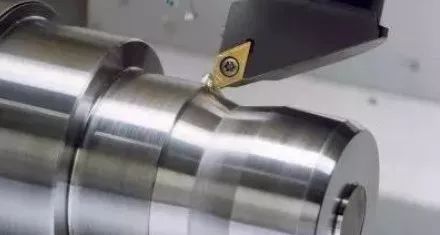
Torneaketa ebaketa-prozesu bati egiten zaio erreferentzia, non piezak biratzen dituen eta torneatzeko tresna plano batean linealki edo kurbatuz mugitzen den, barneko eta kanpoko gainazal zilindrikoak, amaierako aurpegiak, gainazal konikoak, osatzeko gainazalak eta piezaren hariak prozesatzeko.
Tornearen gainazaleko zimurtasuna 1,6-0,8μm-koa da.
Torneaketa zakarrak ebaketa-sakonera handia eta aurrerapen-abiadura handia erabiltzea eskatzen du biraketa-eraginkortasuna hobetzeko ebaketa-abiadura murriztu gabe. Gainazalaren zimurtasuna 20-10um-koa izan behar da.
Erdi akabera eta akabera torneatzeko, saiatu abiadura handia eta jario eta ebaketa-sakonera txikiagoa erabiltzen, eta gainazaleko zimurtasuna 10-0,16 um-koa da.
Fin-fin ehotutako diamanteak torneatzeko tresnak zehaztasun handiko tornuetan erabiltzen dira burdinazkoak ez diren metalezko piezak abiadura handian 0,04-0,01um-ko gainazaleko zimurtasunarekin bukatzeko. Torneaketa mota honi "ispilu biraketa" ere esaten zaio.
Xinfa CNC erremintek kalitate oneko eta prezio baxuko ezaugarriak dituzte. Xehetasunetarako, mesedez bisitatu:
CNC Tresnen Fabrikatzaileak - Txinako CNC Tresnen Fabrika eta Hornitzaileak (xinfatools.com)
2. Fresatzeko zehaztasuna
Fresak piezak mozteko ertz anitzeko tresna birakariak erabiltzeari egiten dio erreferentzia, eta prozesatzeko metodo oso eraginkorra da. Planoak, zirrikitu eta gainazal bereziak prozesatzeko egokia, hala nola splines, engranajeak eta haridun moldeak.
Fresatzeko prozesatzeko zehaztasunaren gainazaleko zimurtasun orokorra 6,3-1,6 μm-koa da.
Fresatzeko gainazaleko zimurtasuna 5-20μm-koa da.
Erdi akabera fresatzeko gainazaleko zimurtasuna 2,5-10μm-koa da.
Fresatzeko gainazaleko zimurtasuna 0,63-5μm-koa da.
3.Plangintzaren zehaztasuna
Planning ebaketa-prozesatzeko metodo bat da, zestagailu bat erabiltzen duena piezaren gainean mugimendu horizontalak eta linealak egiteko. Piezen forma prozesatzeko erabiltzen da batez ere.
Planoaren gainazaleko zimurtasuna Ra6,3-1,6μm da.
Zakarra planifikatzearen gainazaleko zimurtasuna 25-12,5μm-koa da.
Erdi akabera planeatzearen gainazaleko zimurtasuna 6,2-3,2μm-koa da.
Plano finaren gainazaleko zimurtasuna 3,2-1,6μm-koa da.
4.Artezketaren zehaztasuna
Artezketa, piezatik gehiegizko materiala kentzeko urratzaileak eta tresna urratzaileak erabiltzen dituen prozesatzeko metodoari deritzo. Akabera-prozesu bat da eta oso erabilia da makineria fabrikatzeko industrian.
Artezketa erdi-akaberarako eta akaberarako erabiltzen da normalean, eta gainazaleko zimurtasuna 1,25-0,16μm-koa da, oro har. Zehaztasun artezketa gainazalaren zimurtasuna 0,16-0,04μm da.
Ultra-doitasun artezketaren gainazaleko zimurtasuna 0,04-0,01 μm-koa da.
Ispiluaren artezketa gainazaleko zimurtasuna 0,01 μm-tik behera irits daiteke.
5. Aspergarria eta aspergarria
Barruko diametroa mozteko prozesua da, zulo bat edo beste ingerada zirkular bat handitzeko tresna bat erabiltzen duena. Bere aplikazio-esparrua, oro har, erdi-luskatzetik akaberara bitartekoa da. Erabilitako erreminta ertz bakarreko mandrinatzeko tresna izan ohi da (mandrinatzeko barra deritzona).
Altzairuzko materialen aspertzeko zehaztasuna, oro har, 2,5-0,16 μm-ra irits daiteke.
Doitasunezko zulaketaren prozesatzeko zehaztasuna 0,63-0,08 μm-ra irits daiteke.
Argitalpenaren ordua: 2024-02-22