Porositatea, solidotzean gasa harrapatzeaz eratutako barrunbe motako etenak, MIG soldaduran ohikoa baina astuna den akatsa da eta hainbat arrazoi dituena. Aplikazio erdi-automatikoetan edo robotikoetan ager daiteke eta bi kasuetan kentzea eta birmoldatzea eskatzen du;
Altzairuaren soldaduran porositatearen kausa nagusia nitrogenoa (N2) da, eta soldadura-igerilekuan parte hartzen du. Likido-igerilekua hozten denean, N2-ren disolbagarritasuna nabarmen murrizten da eta N2 altzairu urtutik ateratzen da, burbuilak (poroak) sortuz. Galbanizatu/galvanean soldatzean, lurrundutako zinka irabiatu daiteke soldadura-igerilekuan, eta igerilekua solidotu baino lehen ihes egiteko denbora nahikorik ez badago, porositatea sortzen du. Aluminioaren soldadurarako, porositate guztia hidrogenoak (H2) eragiten du, N2k altzairuan funtzionatzen duen modu berean.
Soldadura-porositatea kanpotik edo barrutik ager daiteke (askotan gainazaleko porositatea deitzen zaio). Soldaduraren puntu bakarrean edo luzera osoan ere garatu daiteke, soldadura ahulak eraginez.
Porositatearen arrazoi nagusi batzuk identifikatzen eta horiek azkar konpontzen jakiteak kalitatea, produktibitatea eta emaitza hobetzen lagun dezake.
Gas babesgarrien estaldura eskasa
Gas babesgarrien estaldura eskasa da soldadura-porositatearen kausa ohikoena, gas atmosferikoek (N2 eta H2) soldadura-putzua kutsatzeko aukera ematen baitu. Estaldura egokirik eza hainbat arrazoirengatik gerta daiteke, besteak beste, babes-gasaren emaria eskasa, gas kanalean ihesak edo soldadura-zelularen aire-fluxu gehiegigatik. Bidaia-abiadura azkarregiak ere izan daitezke errudun.
Operadore batek fluxu txarrak arazoa eragiten duela susmatzen badu, saiatu gas-emari-neurgailua doitzen tasa egokia dela ziurtatzeko. Spray transferentzia modua erabiltzean, adibidez, 35 eta 50 oin kubiko orduko (cfh) fluxua nahikoa izan beharko litzateke. Amperaje handiagoetan soldatzeak emaria handitzea eskatzen du, baina garrantzitsua da tasa handiegia ez ezartzea. Horrek turbulentzia eragin dezake pistola-diseinu batzuetan, gas babesgarriaren estaldura hausten dutenak.
Garrantzitsua da kontuan izan behar da diseinu ezberdineko pistolak gas-fluxuaren ezaugarri desberdinak dituztela (ikus beheko bi adibide). Goiko diseinurako gas-emariaren "puntu gozoa" beheko diseinuarena baino askoz handiagoa da. Soldadura-ingeniari batek kontuan hartu behar duen zerbait da soldadura-zelula konfiguratzerakoan.
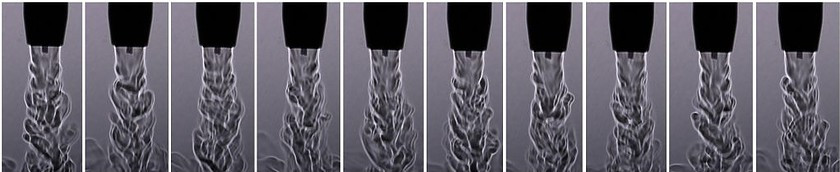
1. diseinuak gas-fluxu leuna erakusten du toberaren irteeran
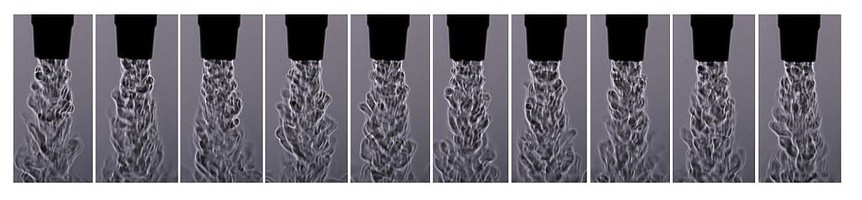
2. diseinuak gas-fluxu nahasia erakusten du toberaren irteeran.
Era berean, egiaztatu gas-mahuketan, osagarrietan eta konektoreetan, baita O-eraztunetan ere, MIG soldadura-pistolaren potentzia-pinean. Ordeztu behar den moduan.
Soldadura-zelula bateko piezak edo operadoreak hozteko haizagailuak erabiltzen dituzunean, zaindu ez direla zuzenean soldadura-eremura zuzendu, non gas-estaldura eten dezaketen. Jarri pantaila bat soldadura-zelulan kanpoko aire-fluxutik babesteko.
Berriro ukitu programa robotikoen aplikazioetan punta-puntarako distantzia egokia dagoela ziurtatzeko, normalean ½ eta 3/4 hazbete artekoa, nahi den arkuaren luzeraren arabera.
Azkenik, bidaia-abiadura moteldu porositateak irauten badu edo kontsultatu MIG pistola hornitzaile bati gas-estaldura hobea duten aurreko osagai desberdinetarako.
Oinarrizko metalen kutsadura
Oinarrizko metalen kutsadura porositatea gertatzen den beste arrazoi bat da - olioa eta koipea errota eskala eta herdoila. Hezetasunak ere susta dezake eten hori, batez ere aluminiozko soldaduran. Kutsatzaile mota hauek, normalean, operadorearentzat ikusgai dagoen kanpoko porositatea eragiten dute. Altzairu galvanizatuak gainazaleko porositaterako joera handiagoa du.
Kanpoko porositateari aurre egiteko, ziurtatu oinarrizko materiala ondo garbitu behar duzula soldadura egin aurretik eta kontuan hartu metalezko nukleodun soldadura alanbre bat erabiltzea. Hari mota honek hari solidoak baino desoxidatzaile-maila handiagoak ditu, beraz, oinarrizko materialaren gainerako kutsatzaileekiko tolerantzia handiagoa du. Biltegiratu beti hari hauek eta beste edozein landarea baino tenperatura antzekoa edo apur bat handiagoa duen eremu lehor eta garbi batean. Hori eginez gero, soldadura-igerilekuan hezetasuna sartu eta porositatea eragin dezakeen kondentsazioa gutxitzen lagunduko du. Ez gorde hariak hotz biltegi batean edo kanpoan.
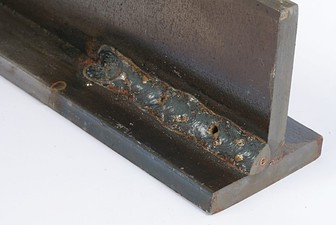
Porositatea, solidotzean gasa harrapatzeaz eratutako barrunbe motako etenak, MIG soldaduran ohikoa baina astuna den akatsa da eta hainbat arrazoi dituena.
Altzairu galbanizatua soldatzean, zinka altzairua urtzen den baino tenperatura baxuagoan lurruntzen da, eta bidaia-abiadura azkarrek soldadura-igerilekua azkar izoztu ohi dute. Horrek zink-lurruna harrapatzen du altzairuan, eta ondorioz, porositatea sortzen da. Egoera honi aurre egin bidaia-abiadura kontrolatuz. Berriz ere, kontuan hartu bereziki diseinatutako (fluxuaren formula) metalezko alanbrea, soldadura-igerilekutik zink-lurrunaren ihesa sustatzen duena.
Tamaina gutxiko toberak eta/edo estutuak
Tamaina txikiagoko toberek ere porositatea eragin dezakete. Soldadura-zipriztinak toberan eta kontaktu-puntaren eta difusorearen gainazalean pilatu daitezke babes-gasaren fluxua murrizten duena edo nahasia bihurtzea eraginez. Bi egoerak soldadura-igerilekua babes desegokiarekin uzten dute.
Egoera hau gehitzen da aplikaziorako txikiegia den tobera eta txirrindulari handiagoak eta azkarragoak pilatzeko joera handiagoa duena. Tobera txikiagoek junturarako sarbide hobea eman dezakete, baina gas-fluxua ere oztopatzen dute, gas-fluxurako onartzen den sekzio-eremu txikiagoa dela eta. Kontuan izan beti kontaktu-puntaren aldagaia toberaren irtenaldiarekin (edo zirrikituan), hori izan baitaiteke toberaren hautapenarekin babes-gasaren fluxuari eta porositateari eragiten dion beste faktore bat.
Hori kontuan izanda, ziurtatu pita nahikoa handia dela aplikaziorako. Normalean, soldadura-korronte handia duten aplikazioek alanbre-tamaina handiagoak erabiltzen dituzten aplikazioek zulo-tamaina handiagoak dituen pita bat behar dute.
Soldadura erdi-automatikoko aplikazioetan, aldian-aldian egiaztatu toberan soldadurako zipriztinrik dagoen eta kendu soldatzaile-aliketak (soldagailuak) erabiliz edo tobera ordezkatu behar izanez gero. Ikuskapen honetan, egiaztatu kontaktu-punta egoera onean dagoela eta gas-difusoreak gas-ataka garbiak dituela. Eragileek zipriztinaren aurkako konposatuak ere erabil ditzakete, baina kontuz ibili behar dute pita konposatuan gehiegi edo luzeegi ez murgiltzeko, konposatu gehiegizko kantitateek babes-gasa kutsa dezaketelako eta toberaren isolamendua kaltetu dezaketelako.
Soldadura robotizatuko eragiketa batean, inbertitu toberak garbitzeko estazio batean edo zurrupagailu batean, zipriztinak pilatzeari aurre egiteko. Periferiko honek tobera eta difusorea garbitzen ditu produkzioko ohiko pausaldietan, ziklo-denboran eraginik izan ez dezan. Toberak garbitzeko geltokiak zipriztinaren aurkako ihinztagailu batekin batera lan egiteko pentsatuta daude, aurreko osagaiei konposatuaren geruza mehe bat aplikatzen diena. Iskinaren aurkako fluido gehiegi edo gutxiegiak porositate gehigarria sor dezake. Toberaren garbiketa-prozesu bati aire-leherketa gehitzeak kontsumigarrien zipriztin solteak kentzen lagun dezake.
Kalitateari eta produktibitateari eustea
Soldadura-prozesua kontrolatzen zainduz eta porositatearen arrazoiak ezagututa, nahiko erraza da soluzioak ezartzea. Hori eginez gero, arku-denbora handiagoa, kalitatezko emaitzak eta ekoizpenean zehar mugitzen diren pieza on gehiago ziurtatzen lagun dezake.
Argitalpenaren ordua: 2020-02-02